Lightweight Cellular Concrete for Geotechnical Applications
Background
Lightweight cellular concrete (LCC) is a mixture of portland cement, water, and air created through a preformed foaming agent. LCC can act as a lightweight, strong, durable, and inexpensive soil or fill replacement for geotechnical applications. Committee 523 of the American Concrete Institute (ACI) defines the product in their publication 523.1R-06, Guide for Cast-in-Place Low Density Cellular Concrete, as “…concrete made with hydraulic cement, water, and preformed foam to form a hardened material having an oven-dry density of 50 pounds per cubic feet (lb/ft3)[800 kilograms per meter cubed (kg/m3)] or less.” LCC is popular in geotechnical applications primarily because it is lighter in weight than soil, is highly flowable and able to fill spaces of any size and shape, and is less expensive than many alternatives.
Applications
LCC in the geotechnical environment can be used for multiple purposes including lightweight road bases and fills, bridge approach embankments, void and cavity filling, pipe and culvert abandonment filling, annular space tunnel grout filling, foundation fills, energy arresting systems, retaining wall backfills, lightweight dam and levee structural fills, landslide repair and slope stabilization, and as controlled density fill.
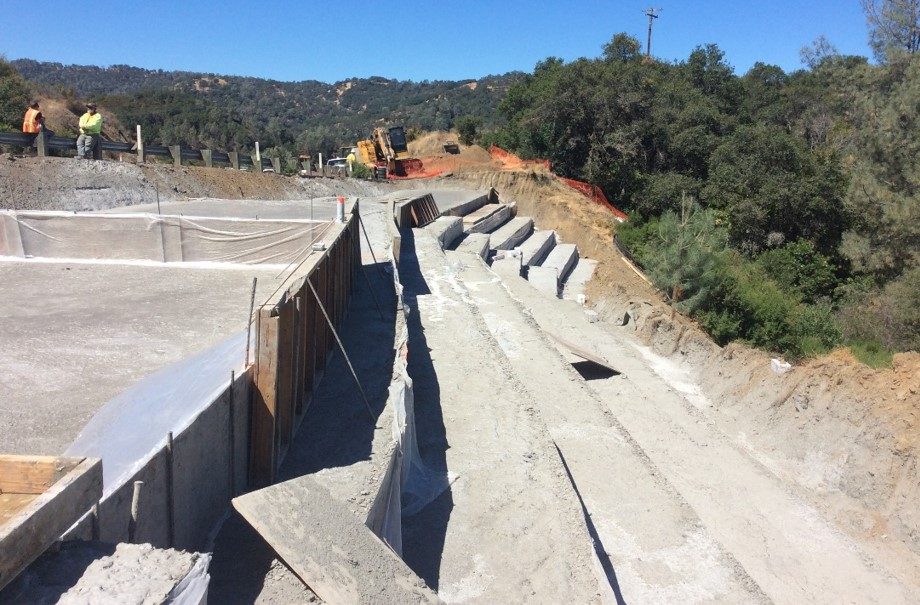
There have been numerous installations of LCC for geotechnical applications with excellent performance across the United States. The material is extremely stable long term and has no known flaws once properly designed and installed.
Properties
Once its ingredients are combined in a mixing chamber and in a fresh state, the LCC material is self-compacting and highly fluid with water-cement ratios (w/c) ranging from 0.35 to 0.80. Water content significantly affects many properties of LCC, especially its strength and viscosity. Field measurement of the unit weight, along with the known w/c of the fresh LCC mixture, are the primary quality control mechanisms. This measurement of the wet LCC is referred to as the cast density and is the density that should be used in the specification and design of the LCC project.
The low viscosity nature of LCC allows for long distance placements and nearly self-leveling installations. LCC viscosity is based upon its water content and the air bubbles present. A commonly used analogy is that the air bubbles increase flowability by acting as tiny ball bearings within the fill. During placement, LCC is assumed to exert hydrostatic force based upon its actual cast density. If a wall or shoring is being backfilled with LCC it should be designed to ensure it has the capacity to support the wet fluid. Since LCC stiffens over time, the hydrostatic force completely disappears as the product solidifies into its final form.
The hardened properties of LCC are what concerns the engineering community the most. These are the properties of the final product and how they perform when in place on the job site. Because LCC is very strong compared to the material it replaces in the geotechnical environment (typically soil and compacted aggregates), the most common hardened property is its unconfined compressive strength. ACI provides a table of industry accepted values for maximum cast density, minimum compressive strength, and bearing capacity for various LCC mixes.
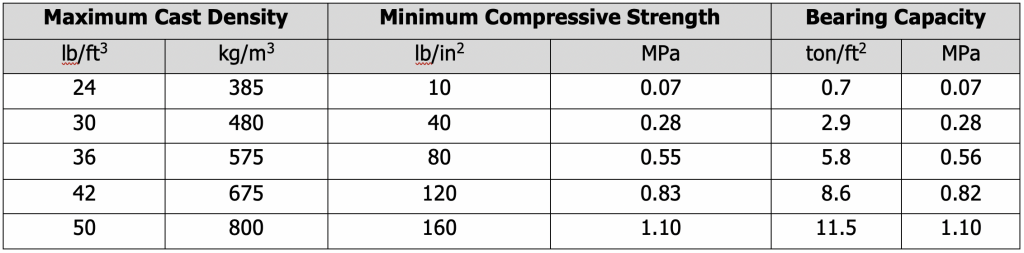
The compressive strength, shear strength, resilient modulus, and California Bearing Ratio of LCC varies due to many factors such as cement quality, type of cement, density, foam quality, w/c, air content, mixing equipment, sand-cement ratio (if sand is added), mix intensity, production and placement temperatures, additives, and more. This list can be expanded because, while LCC has only three primary ingredients, the number of mix variables are immense. Other properties that might also be considered include autogenous (drying) shrinkage, permeability, sorption, heat of hydration, and thermal conductivity.
These variables can lead to an inability to make design decisions based entirely on material property values from tables, figures, and equations. The engineer is encouraged to conduct the necessary testing and consultation with the provider and/or manufacturer to determine the appropriate mixture design for achieving the specified material property requirements.
Considerations
While the most common benefit of LCC is weight/load reduction, there are additional design concerns to consider when used as a geotechnical material. These considerations include bearing capacity, hydrostatic pressure, buoyancy, punching and other shear, design life, seismic, temperature during hydration, drainage, structural number, angle of friction, and pavement support design.
LCC is primarily used because it is lightweight. Its density is typically far less than the density of water, and buoyancy can sometimes be a significant challenge. To account for buoyancy, the level of the worst-case water table, as well as how much of the LCC will be submerged, must be determined. A weight balance calculation is then performed to ensure that the weight above the LCC fill is sufficient to overcome any buoyancy effects.
Materials
While portland cement, water, and preformed foam to create air are the primary ingredients of LCC, additional ingredients may be incorporated into the mixture as long as they do not adversely affect the quality, size, and distribution of the air bubbles. Some common examples include fly ash, slag, silica fume, fibers, gums, accelerators, retarders, or other cement modifiers.
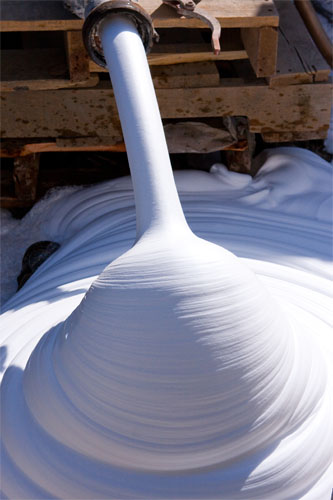
Cement should meet the requirements of either ASTM International (ASTM) C150, Standard Specification for Portland Cement, or ASTM C1157, Standard Performance Specification for Hydraulic Cement; water quality should meet the requirements of ASTM C1602, Standard Specification for Mixing Water Used in the Production of Hydraulic Cement Concrete; and commercially available foaming agents should meet the requirements of ASTM C869, Standard Specification for Foaming Agents Used in Making Preformed Foam for Cellular Concrete.
Construction
LCC is typically placed into its final location utilizing a pump and hose. The LCC is fluid enough to self-consolidate, and there is no vibration required. LCC should not be allowed to set and then be remixed. Instead, it should be kept plastic until allowed to set in its final location. The surface of a hose-placed layer of LCC will be relatively flat with a slight splatter pattern and normally does not require any additional finishing or curing compounds. While superficial cracking may occur on the surface of the LCC, it will not detrimentally affect LCC performance. Where a sloped finish is desired, a grade of up to three percent is possible.
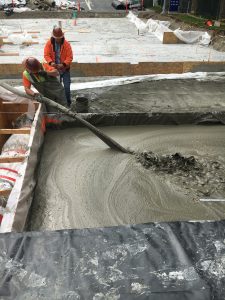
Weather conditions should be monitored before starting the placement of LCC. If heavy rain is imminent, then the placement of LCC should be delayed; however, light rain won’t hurt this product since it is already made of significant amounts of water. Special precautions should be taken if the ambient temperature is below 32°F (0°C) or above 100°F (38°C). High heat can evaporate the water out of the LCC and cause it to excessively shrink. Conversely, cold weather can inhibit the cure time and quality of placed LCC. Placed in moderate temperatures, LCC will set and harden within approximately 10 to 14 hours.
The two types of production systems generally used to mix the cement and water together in LCC are called batch mixing and auger mixing. Batch mixing has long been the industry practice for preparing concrete mixtures. This system of mixing provides all the ingredients necessary to make one “batch” of the product. This works for all types of concretes, including LCC, and any type of batch mixer can be used. Auger mixing is typically performed in mobile volumetric concrete trucks and involves the use of a rotating shaft and flange (auger) to blend the ingredients. The auger receives the raw ingredients at one end, then spins and mixes the ingredients together as they are pushed down the auger.
Most equipment designed for placing LCC utilizes a progressive cavity pump. This type of pump is extremely steady with no pulsing and keeps itself clean on the inside while operating. Peristaltic pumps can also be used to easily transport LCC. This type of pump has the benefit of separating the cementitious materials from the pumping mechanism. Additionally, due to their extreme reliability and strength, piston pumps are used for moving many different types of fluids and slurries, including LCC. Piston pumps utilize a check valve and a piston retracting system, drawing in material, and then pushing it out.
LCC, as with any concrete product, should be carefully observed, inspected, and regulated with the highest quality control available. Small variations in mix designs can cause great differences in the final product, leading to unacceptable materials, failures, and unexpected expenses. Lastly, there is no recommended maintenance of the in-place LCC material itself. After placing and hardening, the material should be protected with some form of surface layer such as concrete, soil, subbase material, drainage mat, etc. Once buried and protected, no additional maintenance is possible or necessary.