Selecting the proper Adhesive Anchor System for Infrastructure Applications
What is an adhesive anchoring system?
An adhesive anchor system is a type of post-installed fastening for attachment of metal to concrete or masonry base material, or new concrete to existing concrete. Adhesive anchor systems are often utilized in conditions where cast-in anchors are missing, misaligned or damaged, or for retrofit projects into existing structures. In several applications, post-installed connections may be favorable to cast-in where jobsite processes are hindered, or safety risks are posed by cast-in elements extending out of the concrete surfaces. In comparison to post-installed mechanical anchors, adhesive anchor systems generally offer greater performance, more flexibility in edge and anchor spacing, and more versatility when compatible with various anchor elements. Adhesive anchors transfer load placed on the anchor element to the base material through bond strength.
The adhesive may be either injectable or in capsule form; this article will focus on injectable adhesives. Anchor elements range from threaded rod and rebar to proprietary or specialty inserts that offer benefits like additional strength, zero cleaning, or temporary attachment. Accessories include the ancillary tools to properly drill and prepare the hole, mix the adhesive to the appropriate ratio, and inject the adhesive completely without air voids.
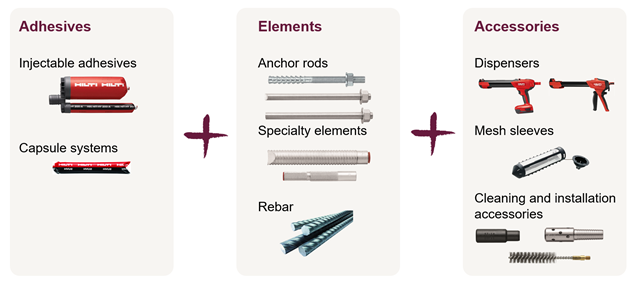
Where are adhesive anchoring connections on civil jobsites?
Although adhesive anchor connections are most frequently associated with building projects, they can be found on jobsites in every infrastructure discipline. Both metal-to-concrete and concrete-to-concrete attachments are ubiquitous across civil engineering projects.
For both structural and non-structural connections, it is important to validate that the adhesive anchor system selected reliably performs in rigorous or adverse jobsite conditions.
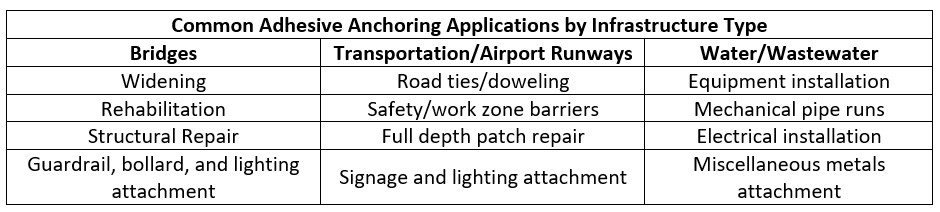
Bridge construction most often sees concrete-to-concrete connections using adhesive and rebar to widen, strengthen, or repair existing bridge elements. Barrier elements like guardrails and bollards, as well as light poles, require robust metal-to-concrete anchorage to brace against impact or withstand high winds.
In roadway projects for motor vehicles or airport runaways, there are concrete-to-concrete connection applications similar to those of bridges. However, in some situations post-installed connections may be required or more heavily relied upon in new construction to accommodate the building project phases. Additional metal-to-concrete attachments include overhead or roadside signage, and miscellaneous attachments, such as those required for temporary barriers for work zones.
Water and wastewater projects see the widest variety of metal-to-concrete attachments as large, heavy equipment and utilities are used to transport fluids and electricity across the project. Post-installed concrete-to-concrete connections may be required during construction due to large loads transferred between concrete members or the building project phases. Many of the post-installed connections in water/wastewater projects are also present in tunneling projects.
How do I select and design the proper connection with an adhesive anchor system?
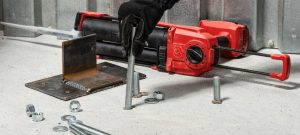
Design provisions for adhesive anchor systems are included American Concrete Institute (ACI) 318-14 Chapter 17 and corresponding testing criteria are defined in ACI 355.4.
There are a wide range of field and loading conditions that should be considered in the design and selection of an adhesive anchor system. When we design a project months–or even years–ahead of construction, it’s intuitive to envision the geometry and load demands on a connection. These include installation orientation of the fastening, geometric constraints like edge distance or base material thickness, and/or application demands like sustained tension or dynamic loading.
Despite the intentions in the initial design phase, field conditions can have a significant effect on the final installed anchor performance. Conditions such as, drilling method, hole cleaning method, and whether water was present or not, all of which influence the performance of the adhesive anchor connection. These conditions are generally incorporated into the analysis and selection of the adhesive anchor system. Communication with the anchor installer is critical to help ensure you’re provided design’s technical data meets the actual field conditions and contractor’s installation method.
For post-installed connections on projects that are subject to state Department of Transportation (DOT) requirements, consult TxDOT’s approved product list for applicable candidates.
One characteristic of infrastructure projects that sets them apart from general building construction is the vast majority of connections are exterior. Civil engineers selecting an adhesive anchor system should pay particular attention to the environment to which these anchors will be exposed to, including moisture from precipitation or condensation, temperature fluctuation from nearby mechanical processes, or corrosive gases from things, such as traffic exhaust. These environmental conditions, both separate or in combination, will cause corrosion of the anchor element and/or a metal fixture being attached. Be thoughtful about the expected life span of the connection and the negative impacts of corrosive environments and consider increasing corrosion resistance of the elements in the adhesive anchor system as needed. Stainless steel, thicker zinc plating for carbon steel, or coating the metal may be needed to preserve the integrity of the connection.
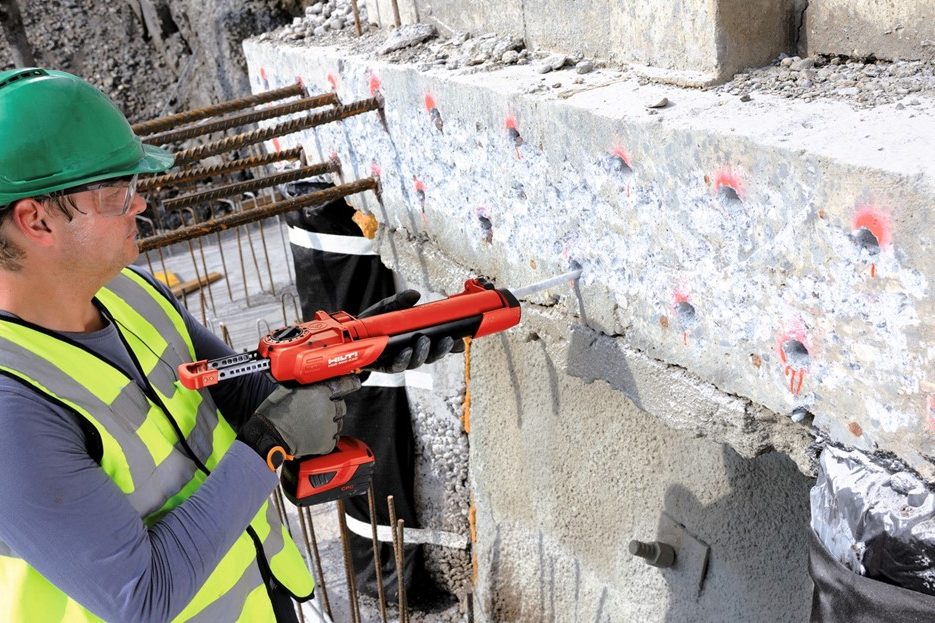
What should I specify when it comes to an adhesive anchor system?
ACI 318 17.8.2.1 acknowledges the bond stress of adhesive anchors is dependent upon a variety of factors and requires structural engineers to consider and include those parameters in their design and specification. There are many factors, but three important and easily overlooked factors are:
- Concrete temperature range at time of installation,
- Moisture condition of concrete at time of installation, and
- Hole drilling and preparation.
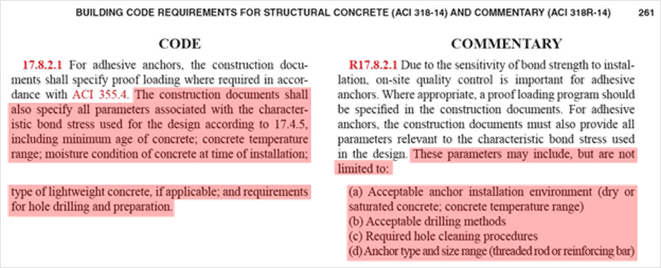
Where can I find information about how these factors are addressed in my adhesive anchor design?
The International Code Council Evaluation Service (ICC-ES) writes acceptance criteria (AC) that reflects the provisions in ACI 355.4 Qualification of Post-Installed Adhesive Anchors in Concrete. ICC-ES likewise publishes an ICC-ES evaluation report (ESR) based on the acceptance criteria testing. These ICC-ESR(s) serve as a third-party evaluation with which engineers can compare engineered products. By meeting the Acceptance Criteria and thus having an ICC-ESR, manufacturers can demonstrate compliance per the referenced model code. Adhesive anchor systems are tested to AC308 Acceptance Criteria for Post-Installed Adhesive Anchors in Concrete Elements.
ICC-ES reports can include a vast amount of information. Below are some suggested sections of an evaluation report that house the most relevant information for a design engineer:
- Check Section 2.0 Uses to ensure the product you’re designing with is intended for your application. Considerations may include, but not limited to, base material type, cracked or uncracked concrete, or development length provisions with rebar.
- Verify Section 3.0 Description includes the anchor element you intend to use; such as rebar, threaded rod or specialty threaded inserts. Additionally, check the adhesive anchor system has been tested with dust-removal systems. While this may not be critical to you in the design phase, contractors will likely be required to meet OSHA 1926.1153 Table 1-compliant systems to better protect against silica dust on the jobsites.
- Read Section 5.0 Conditions of Use for applicable temperature ranges, installation orientations, and any other configuration requirements.
- Read Section 6.0 Evidence Submitted to verify the product you are evaluating has been tested in accordance with ICC-ES AC308.
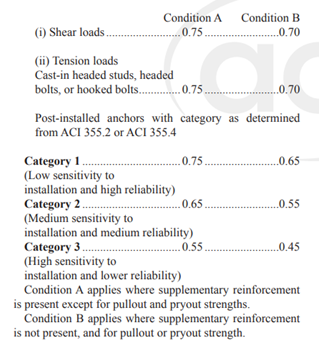
How can these factors influence adhesive anchor performance?
Through reference and reliability testing per AC308, phi-factors are assigned to adhesive anchor products based on anchor diameter, continuous or periodic special inspection, hole-drilling methods, and moisture condition of the concrete. Higher phi-factors are associated with adhesives that perform more reliably and demonstrate less sensitivity to the various conditions.
So why are these three parameters so important?
The criteria for the following parameters can be referenced in ACI 355.4. Corresponding test results can be found in an adhesive anchor’s ICC-ESR and installation parameters can be found in the Manufacturer’s Printed Installation Instruction (MPII).
1) Moisture condition of concrete
When adhesives are installed into concrete holes and cure, they form a bond with the base material to transfer the load from the anchor element into the base material. The presence of water can affect adhesion to the base material. Per AC308, anchors can be tested to varying moisture conditions, including dry concrete, water-saturated concrete, water-filled concrete, and submerged concrete. Each product’s ICC-ESR includes phi-factors derived from testing in these conditions.
What’s important to understand is the two most common moisture conditions and the difference between them. Dry concrete is defined in AC308 as concrete that has not been exposed to water in 14 days. Most regions of North America are likely to experience precipitation, regardless of season, within a two-week period. Even in Texas, mid- to large-sized cities see precipitation on average one out of every three to seven days[1]. If concrete can’t be classified as dry under AC308, it is realistic to assume water-saturated conditions and use the corresponding phi-factor.
2) Temperature ranges
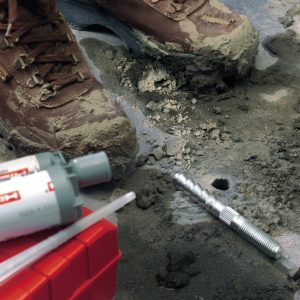
Adhesive anchors cure because of a reaction between a hardener and resin. That reaction can be accelerated or delayed depending on the temperature of the base material. Temperature range impacts the adhesive anchors in four ways:
- Adhesives are tested within a limited range of concrete temperatures at the time of installation. These temperatures are relevant to most installation conditions, but it’s important to verify that the concrete temperature at time at which your anchor is installed is within this range. Concrete temperature at the time of anchor installation can be influenced by geography, climate, and season.
- The time required for the adhesive to cure (cure time) will be longer at colder concrete temperatures and shorter at higher concrete temperatures.
- The time permitted to install an adhesive anchor (working time or gel time) will also vary with concrete temperature. Reference the Manufacturer’s Printed Installation Instructions (MPII) for working times.
- Some products require conditioning to certain temperatures. For example, an ICC-ESR may state the adhesive cartridge must be conditioned to 70°F in base materials less than 70°F in order to achieve performance consistent with the tested data.
Texas sees a wide range of temperatures from the Panhandle to the Gulf Coast and between February and August. All the ways temperature affects an adhesive should be considered when selecting an adhesive anchor system, perhaps the most critical is the work time allowed to install the anchor element into the adhesive during the hot Texas summers. Slow-cure adhesives allow the installer an ample window of time to complete all the installation steps necessary for a reliable fastening.
3) Drilling and hole cleaning
When a hole is drilled into concrete, the hole surface may vary from rough to smooth depending on the drilling method. Additionally, the hole is likely to be filled with concrete dust and debris from the drilling process.
Hole cleaning steps typically consist of blowing out the hole with compressed air, brushing the hole with a steel wire brush, and blowing out of the hole again. This cleaning method can vary depending on the adhesive product. Reference the Manufacturer’s Printed Installation Instructions (MPII) for the cleaning method(s) specific to an adhesive product. Installer training on anchor installation per the MPII is also recommended.
Hilti’s SafeSet System was developed to simplify the hole cleaning steps by using either (a) Hilti proprietary hollow-drill bit and vacuum system that removes dust and debris during the drilling process or (b) a proprietary anchor element, such as a Hilti HIT-Z rod, which requires no hole cleaning to transfer load. Since OSHA’s increased silica dust regulations in 2016, other anchor manufacturers have developed similar technology for the purpose of silica dust removal and compliance with OSHA 1926.1153 Table 1.
As trained and skilled labor is continuously a strained resource, it’s important to reduce complexity of anchor installation process and reliance on installer diligence. Consider systems that don’t require proprietary wire brushes or drill-mounted brushes, that have the greatest flexibility of allowable drilling methods, and systems that keep cleaning steps consistent and concise.
How do I fit all this important information into my anchor specification?
1) Include “Basis of Design” parameters in your General Notes that address the factors that can influence the integrity of your connection.
2) Call out the specific product, anchor diameter and embedment depth, and hole drilling and cleaning method directly in your details.
Adhesive Anchor Systems offer reliable fastening in Civil Infrastructure projects
Across civil disciplines, fastening points are critical to resilient performance for the lifetime of the project. Adhesive anchor systems offer flexibility in both the design phase and when a fix is needed on the jobsite. Familiarity with not only design standards, but also testing methodology and the resulting technical data presented in third-party approvals, is key to selecting and designing reliable connections that withstand demanding jobsite conditions during installation and use.
[1] CurrentResults.com; https://www.currentresults.com/Weather/Texas/average-yearly-precipitation.php
Additional information on Hilti North America can be found here.
Example Use Cases
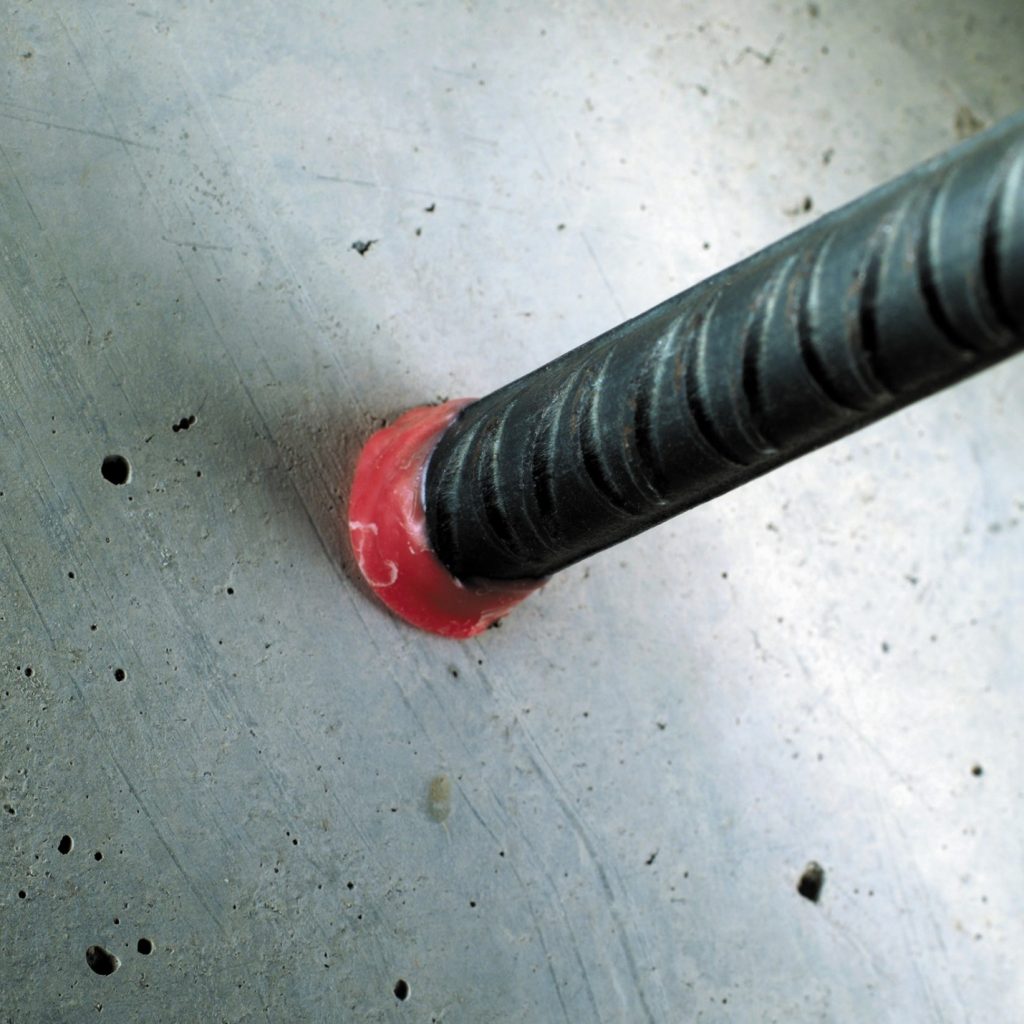
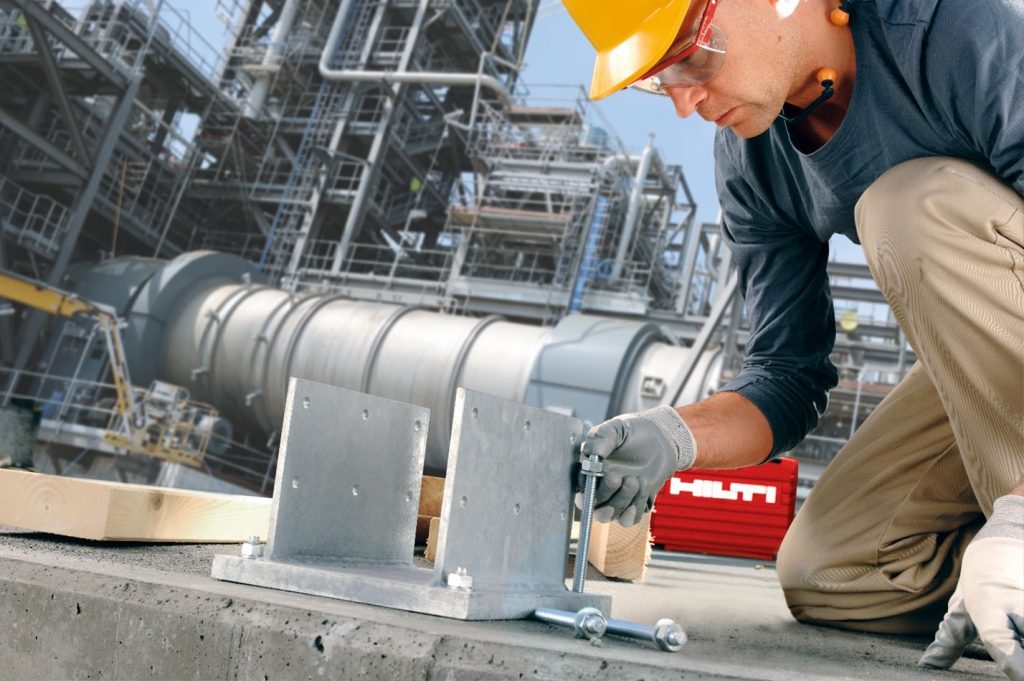
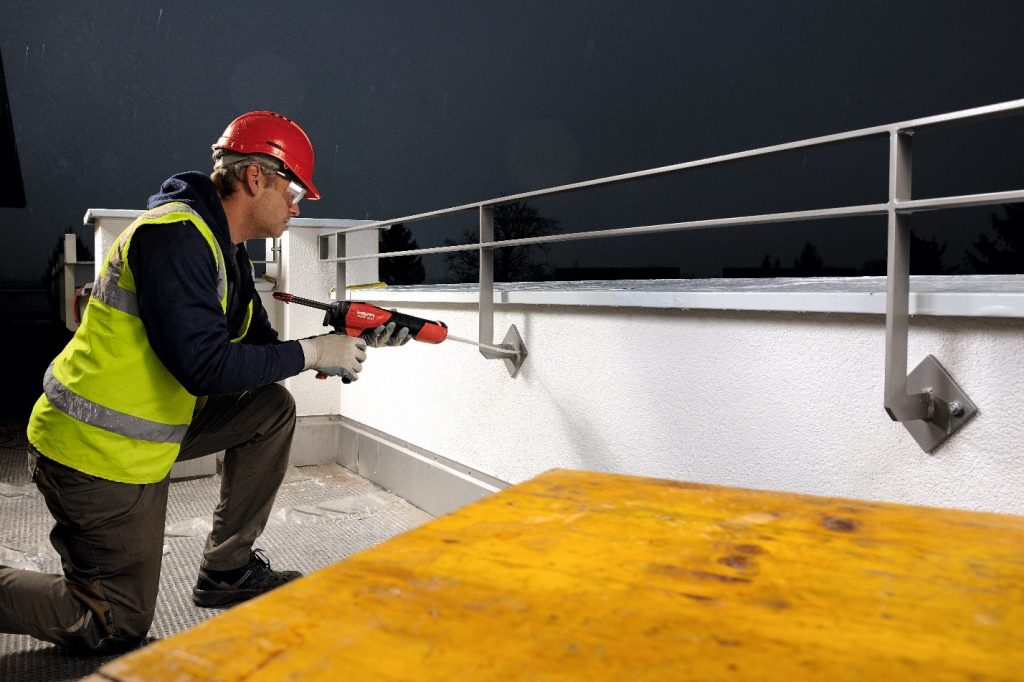
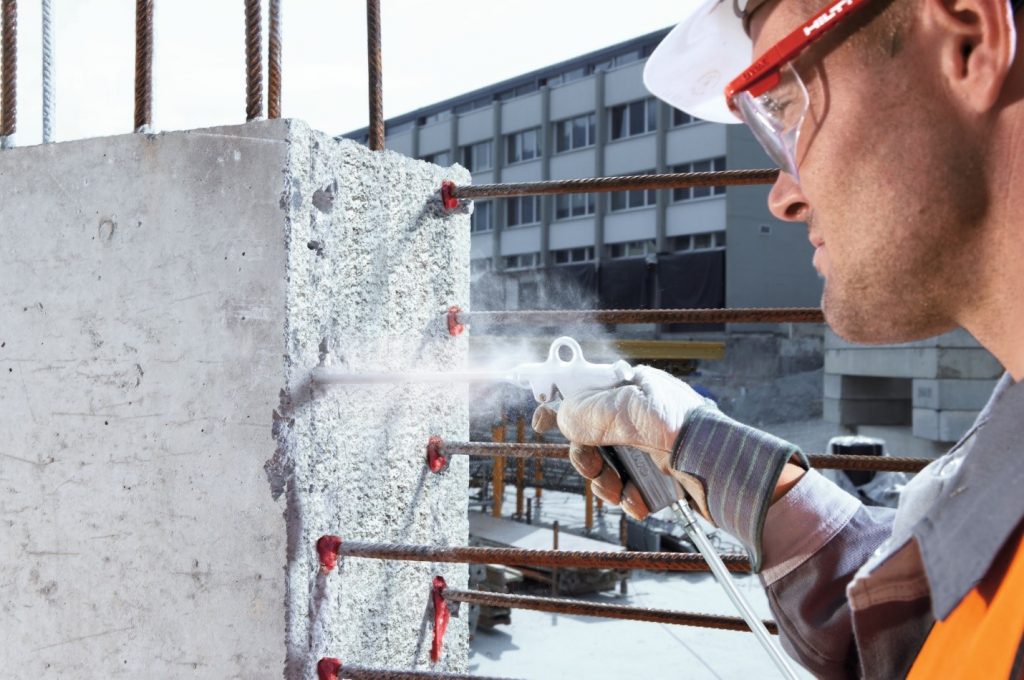
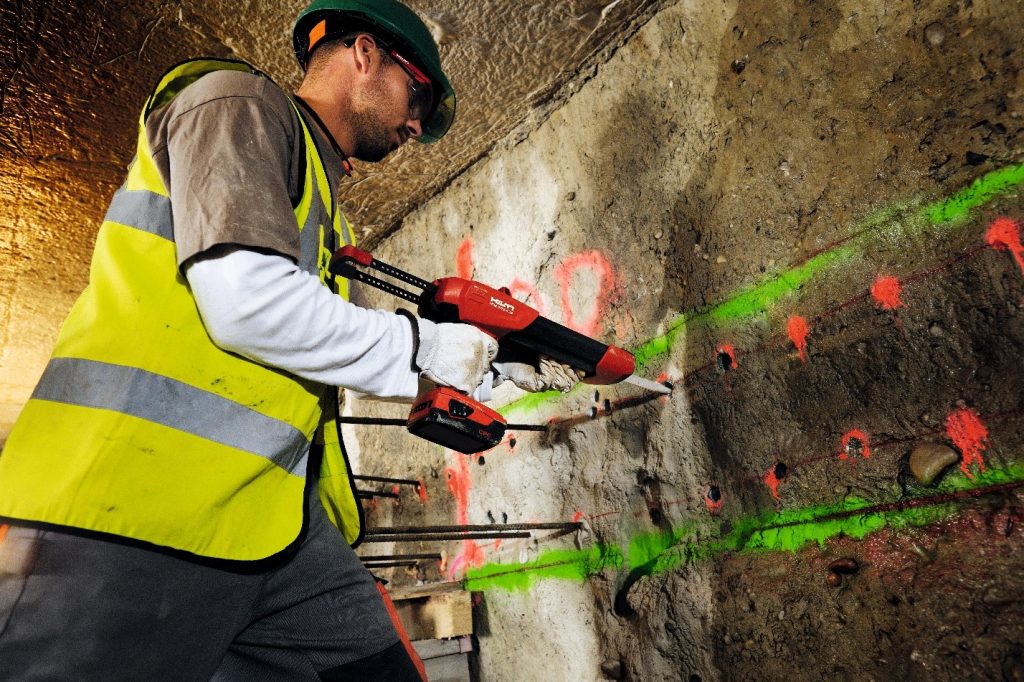
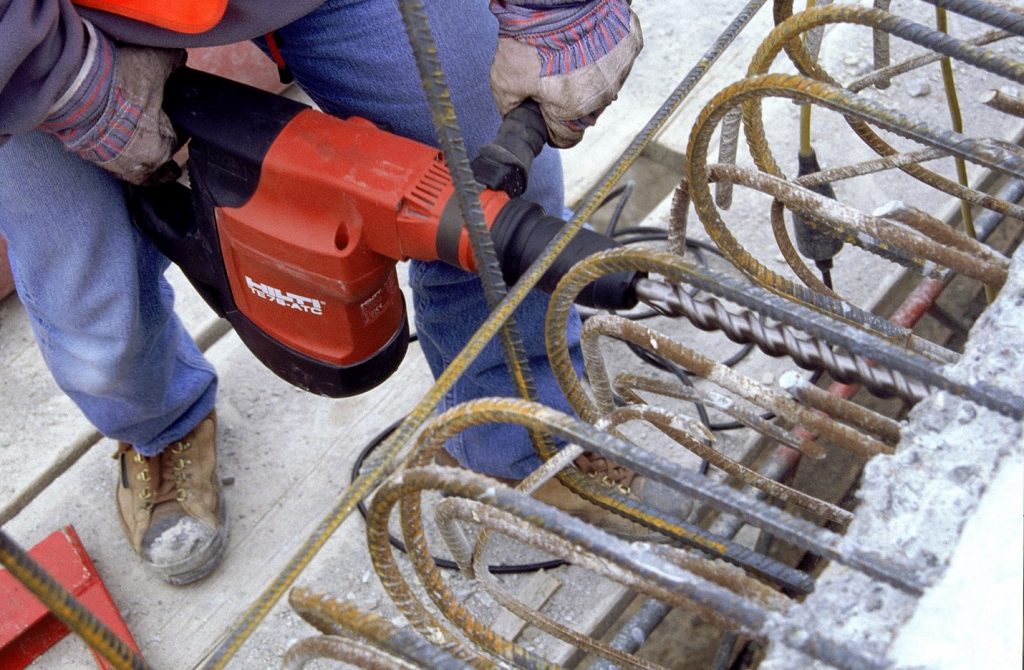